ASSIGNMENT:
ILC was asked to visually inspect 48 test stations reportedly damaged by fire at a manufacturing plant. During the investigation, it was discovered that the insured claimed that 34 critical components and parts were either obsolete, out of date, or no longer available. This claim prompted a proposed redesign of new test stations at a projected cost of $1.6 million. In response, ILC began investigating the availability of parts essential for rebuilding the subassemblies within the test stations, contributing valuable insights to the assessment.
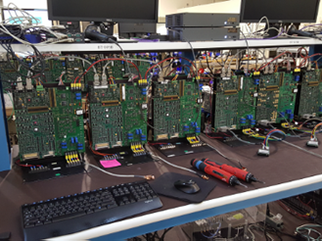
INSPECTION:
- During the evaluation of the 34 parts that were considered unavailable and out of date, ILC was able to confirm that many of the parts WERE available, and for those that were not, there were equivalent substitutions that were of the same Like, Kind, and Quality.
- ILC also provided an analysis of the time required to rebuild the 48 lost test stations, encompassing components such as tables, power supplies, computers, monitors, data cards, barcode readers, and various other parts.
REMARKS:
“Industrial Loss Consultants expertise not only ensured a cost-effective solution but also gave us confidence in their ability to deliver results under challenging circumstances.”
-Adjuster, Major Insurance Provider
SOLUTIONS:
- Following a comprehensive analysis, ILC determined that all 34 parts originally considered to be unavailable, yet essential for rebuilding the test stations, were indeed available. ILC was able to procure components with low availability for only $16,753.
- After a complete evaluation and procurement of the necessary parts to complete the reconstruction of the test stations, completion costs totaled $150,360.
- Additionally, ILC estimated the labor required for the rebuilding and installation process to be approximately 2,439 hours, with an average labor cost of $60 per hour, resulting in a total labor cost of $146,340.
RESULTS:
- After combining labor and material costs, ILC arrived at an estimated total test station rebuild and installation cost of $300,540.
- A cost savings of $998,920 from the original estimated cost of $1.6 million.