ILC ASSIGNMENT:
When three printing presses were damaged by a lightning-induced power surge, the insured’s manufacturing plant was presented with a major dilemma. The presses were outdated and could not be replaced with original equipment manufacturer parts making the matter worse. Due to this situation, the insured was faced with a significant claim loss, including the possibility of a Business Interruption Claim that could exceed one million dollars. In addition, the unavailability of OEM parts increased the cost of replacing the equipment to more than $3 million, adding to the potential $4 million claim total. The severity of the problem made it clear that addressing the damages and potential financial impact on the manufacturing plant would require a thorough and well-thought-out strategy.
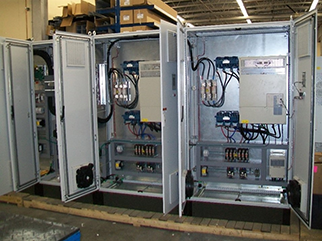
INSPECTION DETAILS:
- Using its extensive experience in the printing industry, ILC verified that the insured’s chosen vendor was qualified to repair the equipment.
- To prevent a total loss, ILC assisted in sourcing aftermarket parts, enabling the equipment to be repaired to its pre-loss state.
- The cost to restore the equipment to pre-loss condition was only $100,000, compared to a complete replacement cost of $3 million.
- ILC’s intervention not only mitigated the financial impact but also limited Business Interruption costs, offering a more cost-effective solution than investing in entirely new equipment.
SUMMARY:
- Verified that lightning struck in the area on the day of the loss, establishing a direct link between lightning and power surges.
- Confirmed that the insured’s vendor was qualified to complete the necessary repairs to the fire-damaged equipment.
- Assisted in locating the specific parts required for equipment repairs and ensuring their availability.
- Project managed the entire repair process, overseeing the work from start to finish to ensure a thorough and effective restoration.