“ILC’S PROJECT MANAGED THE ENTIRE REPAIR PROCESS BY INTEGRATING MULTIPLE MECHANICS, ENGINEERS, AND CREWS TO BRING THE ENTIRE OPERATION BACK TO PRODUCTION WITHIN SIX MONTHS.”
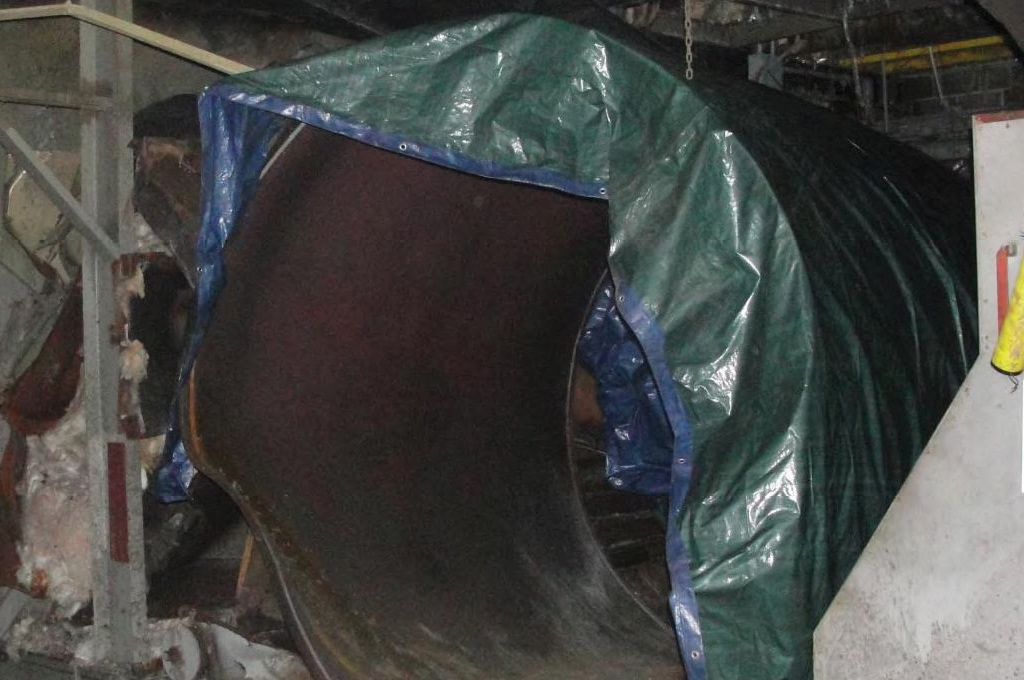
CLAIM DETAILS
An explosion occurred within a curing station inside a production line built to produce a 90-100” foam board for finishing. Production required high volume, continuous delivery. The curing station included a gas-fired steam dryer. Business Interruption was estimated at a rate of $1.6 million per month, and options were limited for outsourcing production short term.
COMPLICATION
The Original Equipment Manufacturer (OEM) was no longer in business and the entire line lacked documentation. Upon inspecting the curing station, ILC consultants determined the station to be “unsafe and inappropriate” for repair. Replacement of the entire line with Like, Kind, and Quality (LKQ) parts was estimated to take up to 16 months at an approximate cost of five million dollars.
ILC VALUE-ADDED SOLUTION
ILC provided an assessment within seven days that included a comprehensive evaluation of the entire warehouse, production line, and employee workspace. ILC recommended rebuilding what could be salvaged from the line and integrating a safer solution for the steam dryer. This approach allowed Like and Kind quality production with a different dryer which was safer and easier to maintain than the original dryer. The cost to rebuild and replace was $3.25M and ILC’s consultants oversaw the process integrating multiple mechanics, engineers, and crews to restore full production within six months.
RESULTS
- A credible plan for restoration to pre-loss production capacity utilizing a different method of curing the product in the form of a used Hot Air Flotation Drying System.
- The solution provided by ILC helped to save the client almost 12 million dollars in Business Interruption expenses and avoided the timely process required to replace the entire line.
- ILC Project Managed all aspects of the job communication with both the insured and the third-party adjusting firm which helped to streamline the communication between all parties.