Project Management
Each consultant has an in-depth understanding specific to the process and equipment used by the insured – spanning a wide breadth and depth of machines and processes.
Reduction in Business
Interruption Re-Engineering the Technology Platforms
Re-Engineering the Technology Platforms
Specific to bringing pre-dated technology and functionality up to current code, adhering to safety and code regulations.
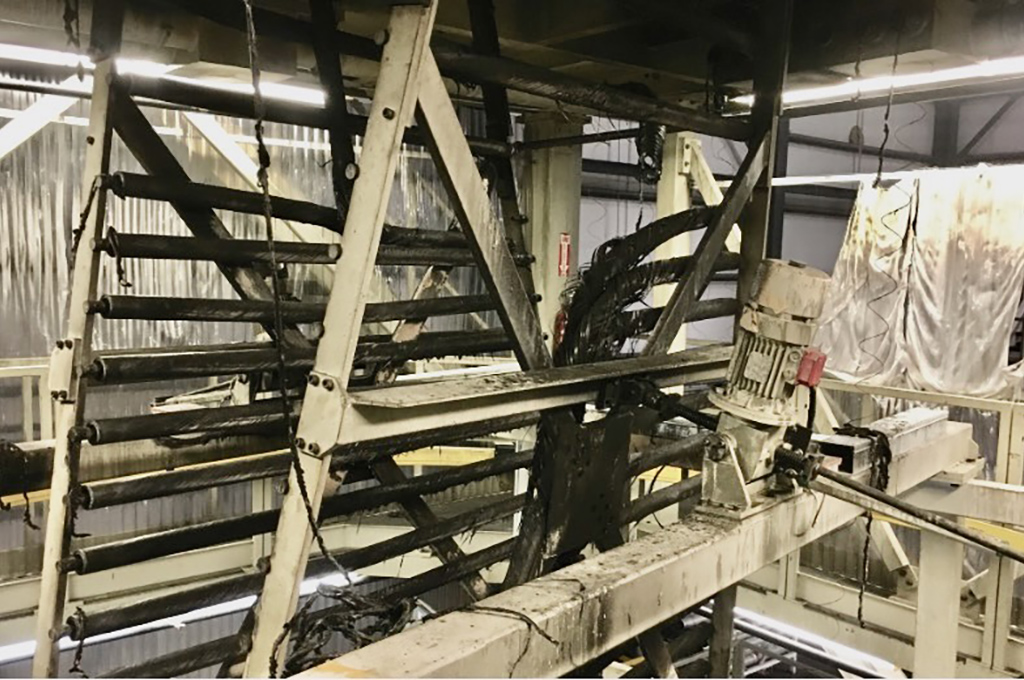
The insured experienced a large fire loss to a unique line. The OEM was European in origin and was out of business for over 10 years. The line was one of only 10-12 in all of North America. The total height of the line (all machines and processes included) was 7 stories tall. The line itself required processes that were not intuitive and had unexpected methods for set up.
COMPLICATION
The cost of a new machine was estimated to be $3.5MM and it was determined it would take 18 months to deliver. Due to the nature of the construction for a new line, the plant would have been required to reduce production capacity to 50% on the second line to both remove and install a new line. With one line completely lost, and a second at reduced capacity of 50%, the
business interruption would have been greatly compounded.
Between the fire loss damage to key parts of the unique, undocumented line and the fact that the OEM was no longer in operation, there was a lot of lost information needed to deliver a rebuild. The rough order of magnitude determined at the first site review compared to the additional detailed inspection varied greatly due to the non-intuitive nature of the line set up.
SOLUTION
ILC was the first consultant on site after the loss. A complete line review starting with the 7th level down to the ground was completed. ILC’s team sought out individuals from the original OEM to procure what detailed information was still available. ILC performed it’s 9 step process
to determine the repair procedures required. The mandatory electrical check was leveraged to provide details of areas that were effected but not visible. ILC’s expert consultants were able to provide an initial rebuild estimate 72 hours after completion of the detailed inspection.
After researching original OEM inputs and creating an assessment for reverse engineering, a rebuild timeline was estimated at 4 months, with minimal invasive impact to the remainder of the plant, its production, or management. Cost ROM (rough order of magnitude) was
established at $1.9MM after the detailed inspection. In the end, ILC’s solution delivered:
- Contact with original OEM individuals, which helped streamline needs during the rebuild process specific to fire loss areas.
- Simple, easy, pragmatic decision making on rebuild vs. new for the insured at an obvious time of crisis and information loss.
- An estimate for time and costs that remained stable from initial rebuild assessment to final rebuild completion.
- A one-stop solution across assessment, reverse engineering, and non-invasive site and project management.
- The insured was able to keep their business running efficiently, despite reduced capacity and with complete concentration.
- Weekly updates to keep the carrier, insured and ILC team in sync at all time.
Due to ILC’s recommendation and solution, the following results were accomplished:
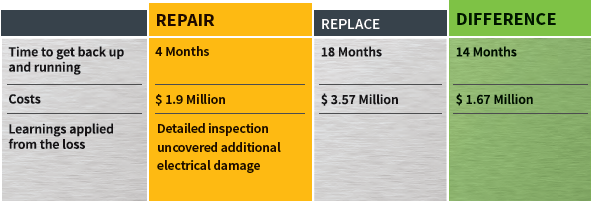