We saved our client over $400,000 by identifying pre-existing conditions.
ILC ASSIGNMENT:
After a flood incident, ILC was assigned to conduct a comprehensive inspection of the mechanical rooms at an indoor water park resort. A complete assessment of the mechanical rooms that housed the motors, and pumps, water conditioning equipment, and electrical distribution system was necessary. The insured was claiming that the entire electrical distribution system needed replacing at an estimated cost of materials alone at $260,000.
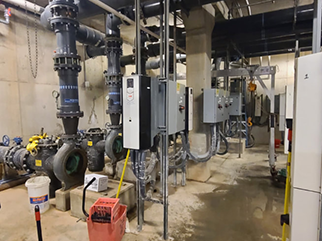
ILC INSPECTION DETAILS:
- As a result of ILC accessing the site immediately after the flood, our consultants were able to identify the damaged electrical distribution equipment.
- Corrosion on electrical distribution equipment was identified above the high-water line predating the most recent flood event.
- The identified corrosion was attributed to the prevailing working environment, specifically chlorine vapors in the mechanical and electrical rooms.
SOLUTIONS:
- ILC learned that the electrical repair contractor provided a $500,000 quote to replace all electrical equipment where corrosion was evident, regardless of whether the corrosion occurred before or after the most recent flood event.
- Leveraging ILC’s identification and documentation of the pre-existing conditions throughout the water park, the restoration costs attributed to the flood event were successfully REDUCED to $90,000.
- In addition, the water park’s downtime to provide the necessary repairs was also REDUCED to only two days, resulting in significant cost savings for our client and minimizing business interruption.
RESULTS:
- By uncovering damaged equipment that occurred prior to the loss, we saved our client 82% in repair costs.
- A 2-day turnaround helped keep the business running smoothly!
ILC DIFFERENCE:
Damage to equipment and machinery in a manufacturing plant can severely impede an insured’s capacity to fulfill order deadlines and maintain customer satisfaction.
The inner workings of these facilities, including components, and parts, is crucial to determining whether rebuilding or replacing damaged equipment is the most viable option. With over 30 years of experience, the machinery and equipment consultants at ILC excel in this domain like no other in the industry.
If you seek outstanding service, precise answers, and effective solutions like this case study, the next time your claim requires the knowledge and experience in machinery and equipment consulting, reach out to the experts at ILC!