DESK REVIEW OF DAMAGED CAR WASH SYSTEMS
A detailed review of car wash equipment loss and replacement saved our client $32,000.
ILC ASSIGNMENT
A Car Wash Machine valued at $316k sustained significant damage after being struck by a vehicle, rendering it reportedly beyond repair.
ILC was contacted to conduct a desk review of submitted documents regarding the claim to determine whether the car washing machine could be repaired and the associated costs. ILC was also asked to investigate the claim that replacement parts from the manufacturer’s authorized dealer were unavailable.
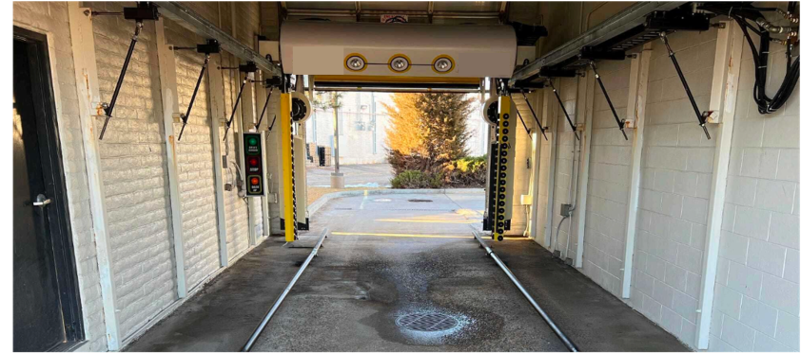
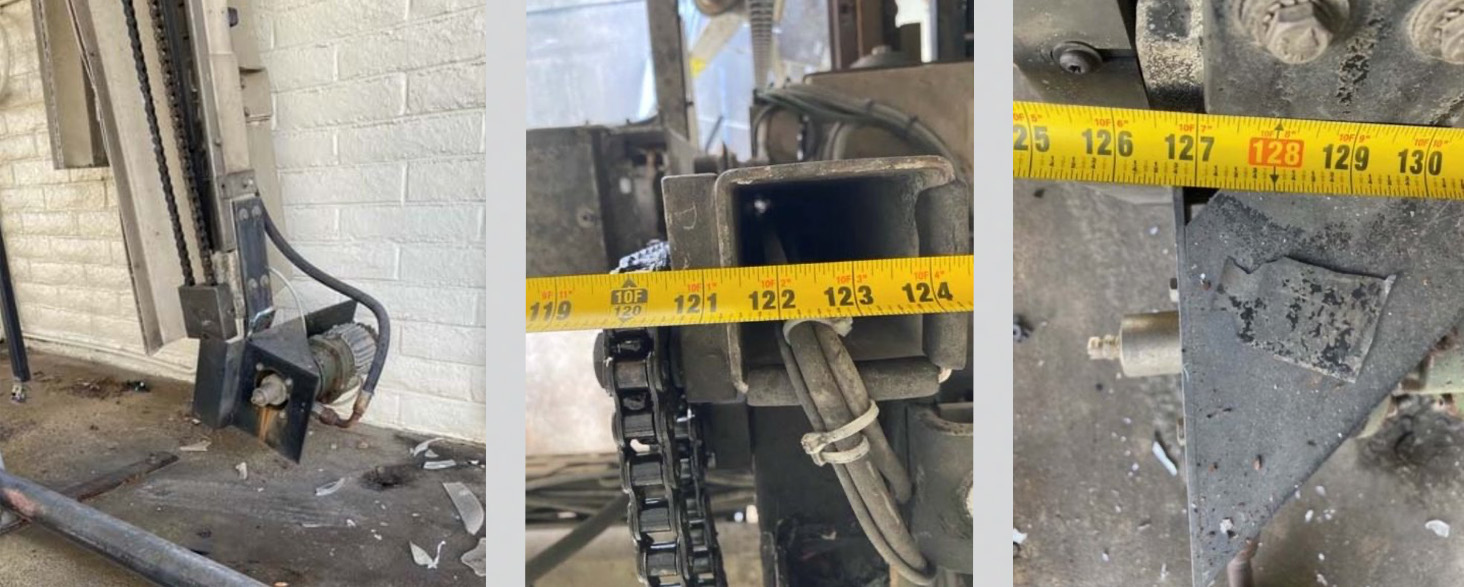
INSPECTION
- Although this was a desk review, it proved as challenging as many field inspections, primarily due to the possibility of subrogation.
- Because the car wash equipment was originally manufactured in Germany, it was challenging to navigate a complex communication loop between the manufacturer and the U.S.-based sales / service representatives.
- Complicating matters further, the damaged equipment had been scrapped without any parts being salvaged. ILC was able to obtain photographs from the subrogation adjuster to move our investigation forward.
- Additionally, the car wash owner was unreachable, and the business was listed for sale shortly after the replacement of the equipment.
SOLUTIONS
- The damaged car wash equipment was reportedly replaced at a Replacement Cost Value (RCV) of $315,929.20.
- An invoice totaling $115,929.20 was provided toward the RCV, referencing a past equipment contract; however, the referenced contract was not supplied.
- Typically, we would apply a depreciation limit of 50% of RCV for previously serviceable equipment. However, in this instance, considering the technical obsolescence and the fact that the 8-year-old system had no scrap value according to the manufacturer’s representative, we calculated the Actual Cash Value (ACV) at $126,371.68, reflecting a 60% depreciation.
- Our investigation also revealed that the replacement equipment represented an upgrade over the original system, which ILC was able to factor into our calculations for our client.
RESULTS: $31,593 REDUCTION
This reduction was a result of incomplete invoicing and 60% depreciation instead of the normal 50% due to the lack of salvageable parts on the equipment.
ILC DIFFERENCE
Damage to equipment and machinery in a manufacturing plant can severely impede an insured’s capacity to fulfill order deadlines and maintain customer satisfaction.
The inner workings of these facilities, including components, and parts, is crucial to determining whether rebuilding or replacing damaged equipment is the most viable option. With over 30 years of experience, the machinery and equipment consultants at ILC excel in this domain like no other in the industry.
If you seek outstanding service, precise answers, and effective solutions like this case study, the next time your claim requires the knowledge and experience in machinery and equipment consulting, reach out to the experts at ILC!