ILC Difference:
Project Management
Each consultant has an in-depth understanding specific to the process and equipment used by the insured – spanning a wide breadth and depth of machines and processes.
Reduction in Business Interruption
Capability to manage costs and time to restore the equipment predictably and dependably.
Re-Engineering the Technology Platforms
Specific to bringing pre-dated technology and functionality up to current code, adhering to safety and code regulations.
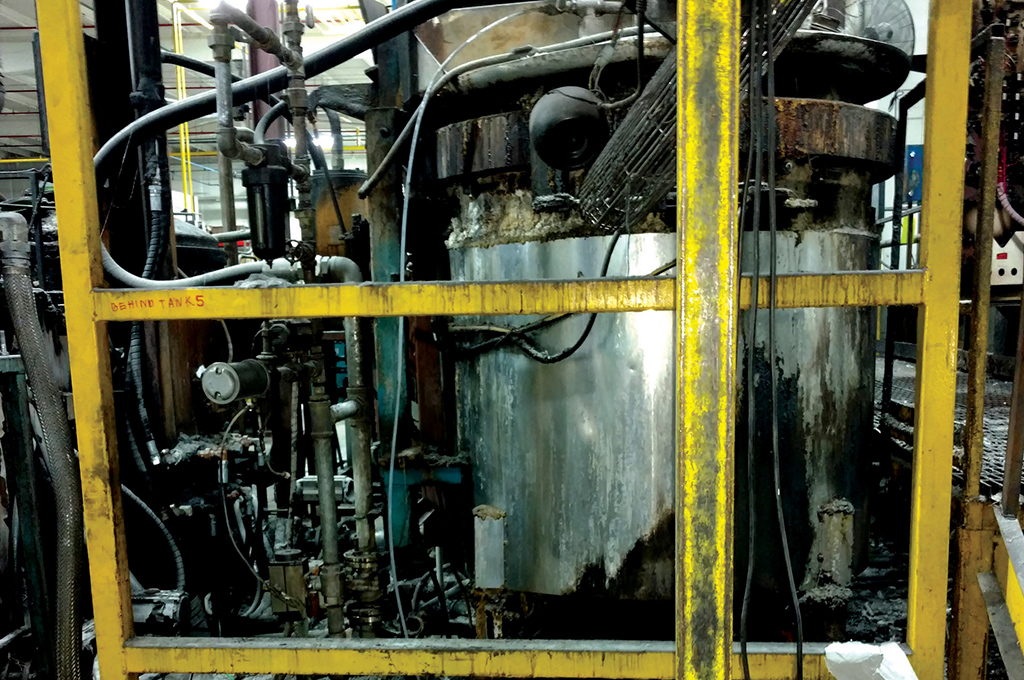
SITUATION
While repairing a resin tank at an automotive casting plant, a fire broke out when the residual resin was accidentally ignited by a torch. As a result, the power supply in the plant was disrupted, causing the high-production resin line to cool down and stop functioning. This sudden halt in operation led to the solidification of the entire line, including the tanks and all related equipment.
COMPLICATION
The pressure vessels and other equipment, which dated back to the mid-1960s and mid-1980s, did not have an original equipment manufacturer. Over the years, most of the equipment on the production line had been modified and customized to suit the insured’s application. Despite the installation of a new comparable system at another facility, they encountered operational difficulties in achieving the desired results and outcomes.
After evaluating the progress of the new line installation, the consultants at ILC discovered that there was a significant lead time required to build a new line. To meet customer commitments, the insured required an immediate solution to restore the line to full production quickly.
SOLUTION
ILC’s consultants were engaged to assess the damaged equipment, collaborating with the insured and the client adjuster on-site. Based on the assessment, it was determined that the machinery could be restored to its pre-loss condition within a specified timeframe. To expedite the restoration process and quickly return the rebuilt tanks and machinery to the insured’s site, ILC partnered with a specialized restoration company. This strategic partnership involved a team of experts dedicated to efficiently restoring and recertifying the equipment with a specific focus on the pressure vessels, to resume production promptly.
ILC’S SOLUTION, REPAIR VS. NEW, NETTED $1.5M SAVINGS WHILE LIMITING BUSINESS INTERRUPTION.
To adhere to the specified 5-month timeline, ILC collaborated directly with loss consultants and engineers who specialized in resin tanks and casting lines. They made adjustments to the location and operations, addressing safety concerns through enhancements in electronics, machine equipment, and the installation of pressure vessels below ground. The project also involved replacing all electronics, pneumatics, hydraulics, plumbing, programming, and safety infrastructure. This was done to ensure compliance with updated safety requirements per code, as requested by the insured. ILC’s solution to repair instead of replace the equipment helped save $1.5 million while limiting business interruption.
Due to ILC’s recommendation and solution, the following results were accomplished:
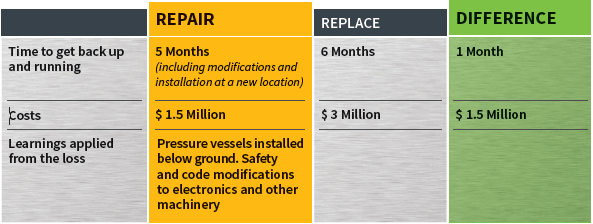